Rare earth elementary school —
New mines are coming, but the potential for recycling is huge.
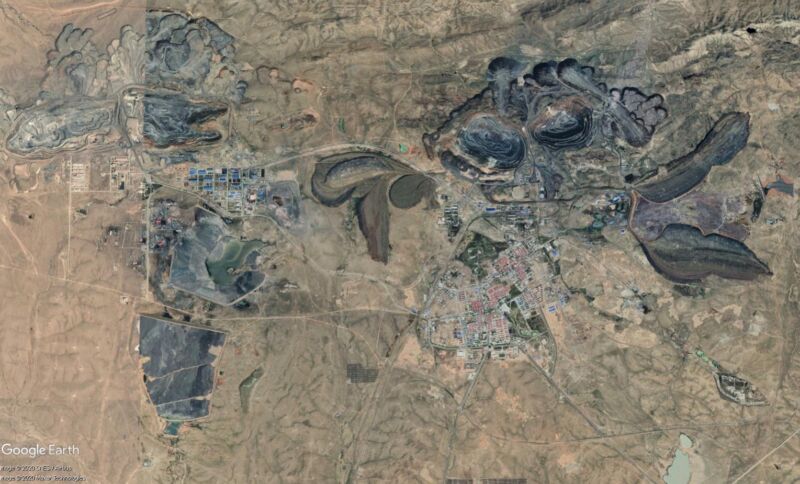
Enlarge / China’s Bayan Obo mine currently produces about half the world’s supply of rare earth elements.
Google Earth
The transition to electric vehicles and renewable sources of electricity, now gaining serious momentum, is largely about dispensing with fossil fuels. But in order to end our reliance on those substances, we need a growing supply of other materials—things like lithium and rare earth elements. Unlike fossil fuels, however, these materials need not be consumed when we put them to use. In principle, devices can be recycled at end of life to return these precious materials to a closed loop that could eventually minimize the need for mining.
But with solar arrays, wind turbines, and electric vehicles starting to hit the disposal stage in increasing numbers—while manufacturing skyrockets—is a new recycling industry actually ramping up to take advantage? The answer is “not really” for reasons both familiar and novel. A lot of heavy lifting remains between here and a closed loop for clean energy technologes.
I prefer my earths medium rare
The so-called “rare earth elements” (or REEs) include the 15 lanthanide elements on the periodic table—lanthanum through lutetium—plus scandium and yttrium straight above them. Despite the name, most of the rare earths are more common than gold or silver in the Earth’s crust, although high-quality ores are indeed hard to come by.
The REEs do, however, confer minorly miraculous properties to electronics and energy tech. Neodymium or samarium in magnets, for example, greatly increases their potency, allowing those components to shrink in size. Rare earths are also used to create the phosphor coatings inside fluorescent light bulbs that are responsible for the color of light emitted. And they’re important for lasers, optics, nickel-metal-hydride batteries—even chemical catalysts for oil refining. For one reason or another, REEs find their way into phones, electric vehicles, solar panels, and wind turbines.
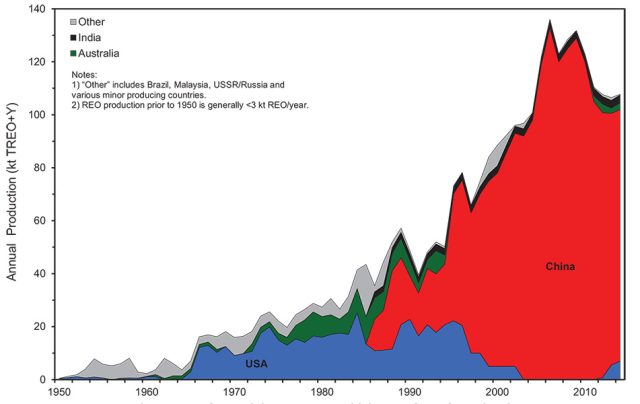
Enlarge / The global production of rare earth elments (including yttrium) has increased drastically—here shown through 2015.
They’re not alone, of course. Wind, solar, and vehicles also rely on steel, copper, aluminum, quartz, lithium, nickel, and cobalt, among other things. Steel, copper, and aluminum already pretty mature recycling industries, so long as these components are collected from the disposal stream. And the lithium supply chain currently gets a lot of attention, from increased mining to battery recycling (which manufacturers are keenly interested in). In contrast, REEs have mainly been discussed in geopolitical terms, since China is responsible for the lion’s share of mining and processing.
Recycling is, in a way, an even more attractive proposition for rare earths than for lithium because of what’s known as the “balance problem.” While you can visit the cereal aisle and select only the cereals you want, rare earth mining means buying the whole aisle. Some of the rare earth elements are much more in demand than others, but the ratios found in ores bear no resemblance to their relative popularity. Looking at the lanthanide series on the periodic table, the elements used most today are found in the middle—neodymium and dysprosium, for example. Most ores, on the other hand, are enriched with one end of the series or the other. They also often contain radioactive thorium and uranium, adding another layer of complexity for mining operations to contend with.
It could be that other elements gain favor in the future, but at least for now, there’s an advantage to getting your rare earths by recycling materials that already contain the mix you want. Otherwise, as demand for dysprosium increases, you could be stuck producing ten times that amount in lanthanum just to get the dysprosium you want.
S’more ore?
Ores with high concentrations of rare earths mostly fall into two general categories: igneous rocks and weathered sediments. The igneous ores are mostly carbonatite—an unusual product of magmas rich in carbonate minerals. It’s unusual enough that there’s only one volcano in the world erupting carbonatite lavas today, although others have in the past.
Something like half of current global rare earth element production comes from China’s Bayan Obo mine alone, which features many carbonatites. Southern California’s Mountain Pass mine along Interstate 15 has exploited similar rocks over its on-again-off-again history.
Australia’s Mount Weld straddles the two categories of rock and sediment. The ultimate source of REEs is carbonatite rock, but current mining is focused on the soil and sediment on top of this rock. That soft stuff is the result of weathering that has broken down the bedrock, carrying away some of the less resilient minerals and further concentrating the rare-earth-rich ones. Similar processes are responsible for deposits of ionic clays in China and of mineral sands in India.
The different sources have different ratios of rare earth elements in them.
“In general, all carbonatites are enriched in lanthanum and cerium,” UNLV’s Simon Jowitt told Ars. “So as you go from lanthanum down towards lutetium, basically the concentrations drop off sharply. In the ionic clays, it’s the other way around; you get far less lights and far more heavies. But what we actually want is some of the stuff in the middle.”
China has dominated production and processing (much of the ore mined elsewhere is still processed in China), although there are many other potential sources. When China attempted to throttle exports amid growing demand in 2011, spiking prices led to a scramble to open new mines. A World Trade Organization ruling in 2014 put an end to China’s restrictions, and together with increased production in other countries and efforts by manufacturers to reduce demand, this re-stabilized the market. But work on new projects has still crept forward, even if some won’t be economical until prices rise again.
Russia, Canada, Brazil, Greenland, and the US all host significant untapped deposits. In the US, for example, there’s the Bear Lodge Project in Wyoming, the Bokan-Dotson Ridge Project in Alaska, and Round Top in Texas—all in the early stages of development. And following on the recent US-China trade war, the US government has pursued funding domestic processing plants in addition to those mines.
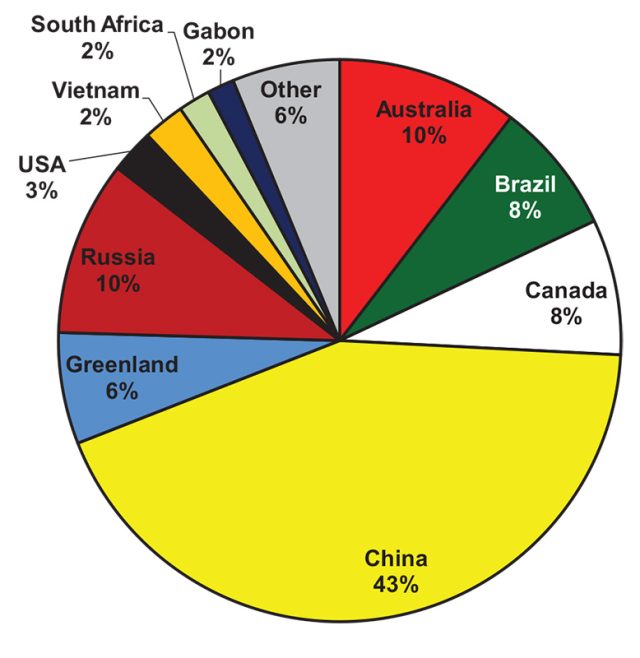
Enlarge / Here’s the breakdown of identified rare earth element deposits.
But it’s not just brand new mines under consideration. Some mines producing other metals have tailings—busted up waste rock—that are full of rare earths. India’s mineral sands mines, for example, have generally targeted things like titanium while putting the rare-earth-bearing minerals to one side. Stenkampskraal in South Africa and Mary Kathleen in Australia similarly have piles left over from uranium and thorium operations.
“There’s the kind of core carbonatite deposits,” Jowitt said. “And then there’s the sort of ‘well these could be interesting if the economics are right…’ And that’s both different types of primary deposits, as well as some of the secondary stuff—the kind of stuff that people aren’t interested in now, but if the prices are right, and waste piles are still there, they may be extractable in the future.”
Reprocessing these stockpiles could be a win-win, as such tailings are often left to leach dangerous substances when exposed to the elements. An economic incentive could get them cleaned up rather than abandoned.